Pultrusion Plant for Top Performance
)
Long Fibre Compounds Based on Engineering Plastics
Powerful Extrusion, Elegant Process
Do you want to produce long-fibre-reinforced thermoplastics more economically?
Especially for the production of lighter functional parts for automotive applications, sports and leisure and the construction industry as well as for safety and functional equipment, the new generation of FEDDEM FLF PT pultrusion lines offer enormous advantages over conventional LFT compounding lines.
The special FEDDEM method not only halves changeover times when threading new rovings but also ensures tight tolerances in glass fibre content in the produced pellets. With FEDDEM’s ICX® Technology and its application to FLF PT turnkey lines, you can produce long fibre compounds based on engineering plastics more economically, more gently and with greater flexibility.
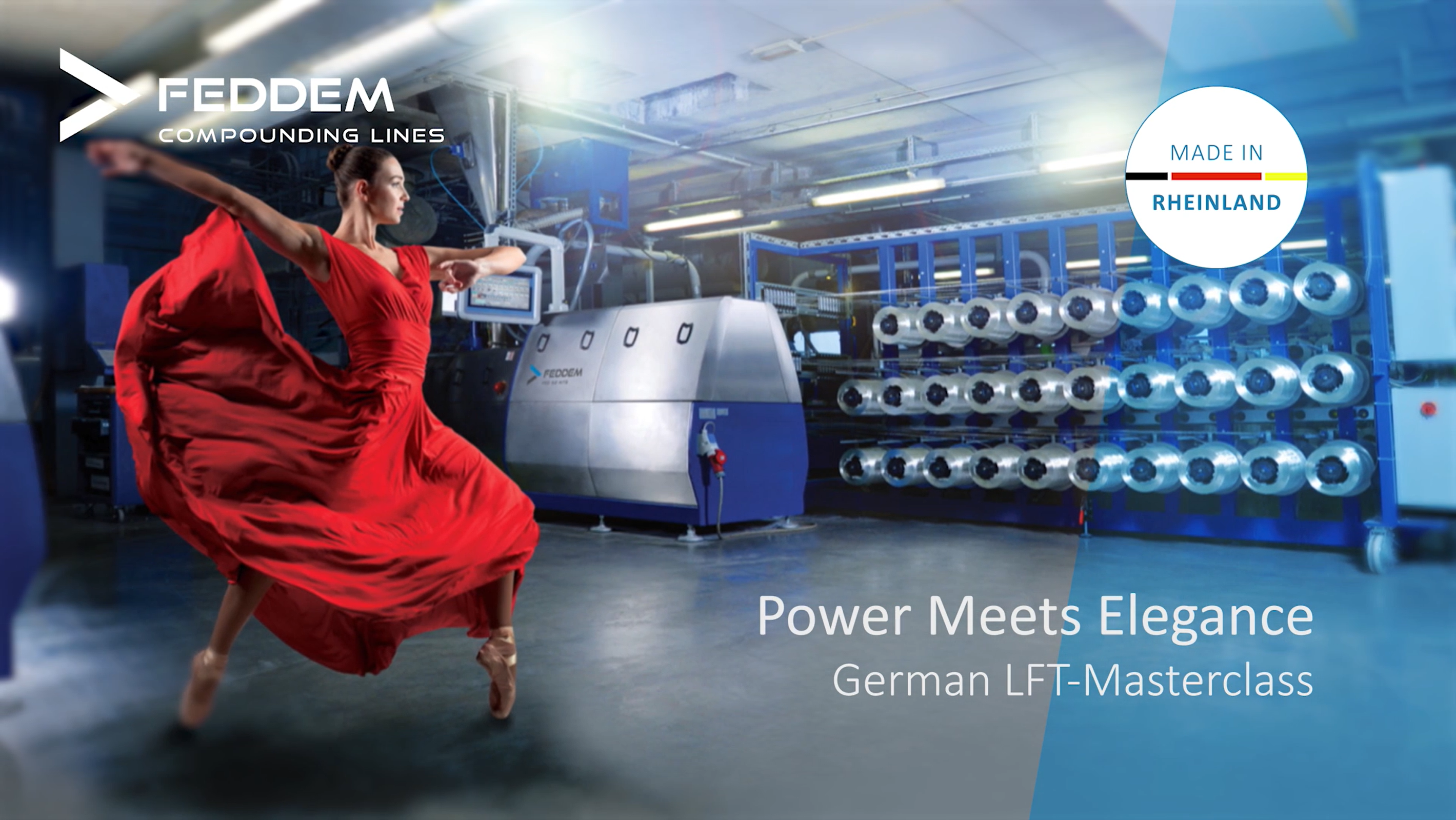
Image dimensions not found
Change image or reupload it
Power Meets Elegance
The high-performance FEDDEM LFT pultrusion line was developed with the special requirements of processing high-quality engineering plastics in mind. The FEDDEM twin-screw extruder is fully enclosed for noise insulation and makes it easy to keep the extruder clean.
At the same time, the full shrouding reduces heat radiation from the extruder’s processing section, thus helping to improve the energy balance of the process. The impregnation technology applied here ensures an optimal bond between polymer and the filaments.
Depending on the formulation, the turnkey line achieves outstanding throughputs at take-off speeds of up to 60 m/min.
German LFT masterclass
The Advantages at a Glance
Delivery as a turnkey plant with system responsibility
Space-saving installation of the line through parallel arrangement of the extruder and roving section – the design of the FEDDEM line components takes into account direct access to maintenance points
Fully automated control processes and overall easy operation
Consistently high quality paired with high throughputs
Narrow tolerances in glass content and best repeatability for repeat orders
Uniform impregnation of the filaments even in the outer areas of the impregnation die
The modular design of the impregnation die in larger FLF-PT lines allows for reducing the number of strands by half with little effort. This enables the line to run at half the throughput rate for processing smaller orders or for producing samples of a new product.
FEDDEM LFT lines are prepared for quick changeover when roving spools must be replaced. This reduces idle times of the FLF-PT line and increases efficiency of the LFT production.
Expert technical support and consulting services are available
Remote maintenance assistance is available via the oculavis SHARE augmented reality system
Do you have questions about our LFT system?
Talk to one of our experts in a personal appointment. Free of charge and without obligation, of course.
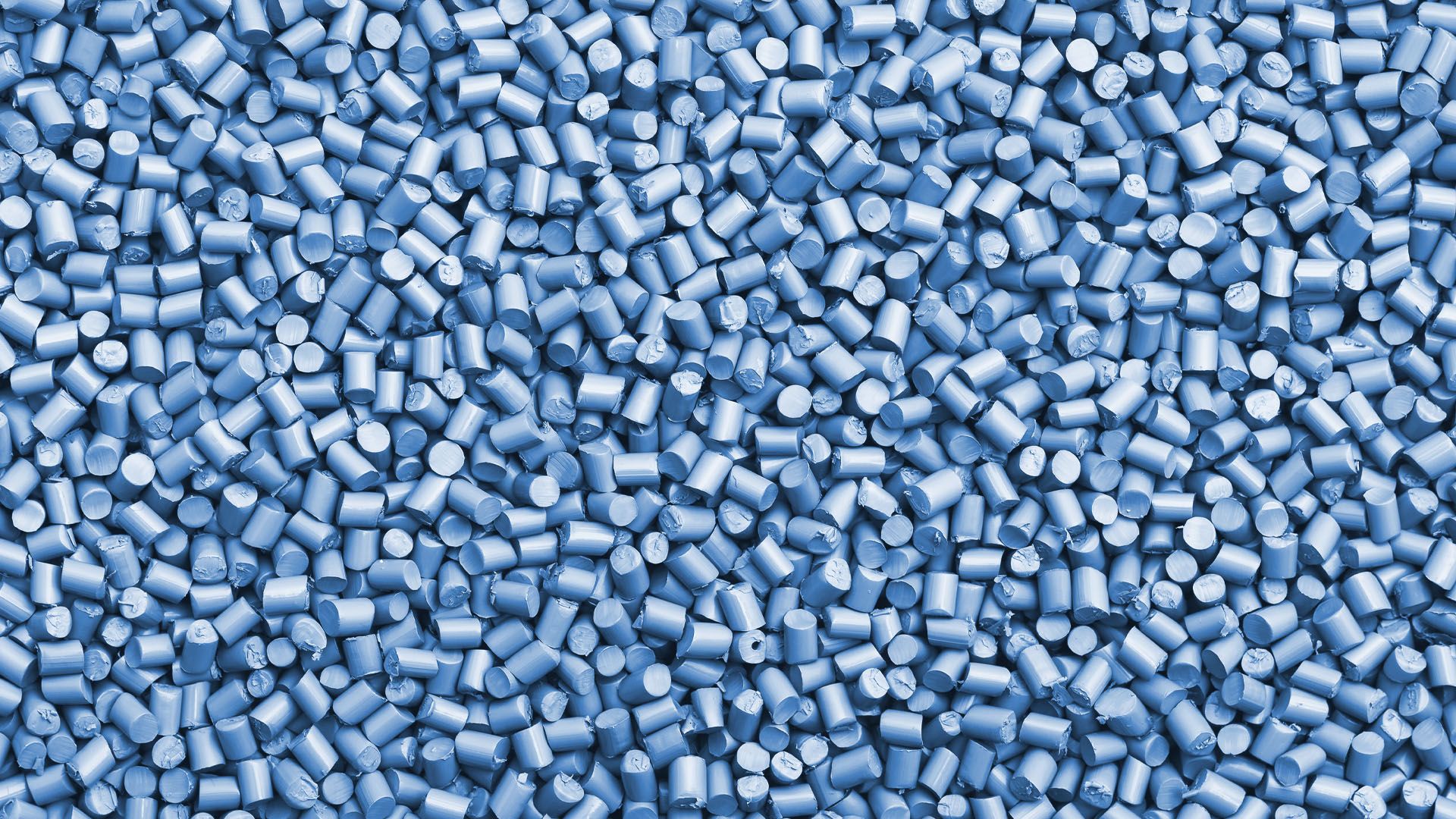
Image dimensions not found
Change image or reupload it
The Importance of Long Fibre Technology
Long fibre thermoplastics, or LFTs for short, expand the range, in which metal components can increasingly be replaced by injection-moulded plastic parts. This is because LFT plastics offer several advantages over conventionally machined metal materials. An advantage over other long-fibre reinforced material: Components made from LFT compounds can be recycled, whereas fibre-reinforced thermoset materials (e.g. epoxy resin based LFT composites) cannot. LFT plastics offer the following advantages over conventionally machined metal materials: More freedom in part design, No corrosion of the part – better resistance to chemical influences than metal, Savings in weight, Cost reduction by eliminating machining steps.
Image dimensions not found
Change image or reupload it
Portfolio of FEDDEM LFT Lines
Currently, we offer two line sizes, which we can modify according to your requirements:
FEDDEM FLF 600 PT and FEDDEM FLF 300 PT.
600/300 = indicates the nominal width of the strand area of the respective line in mm.
Image dimensions not found
Change image or reupload it
Made in Rheinland
FEDDEM extruders are exclusively built in Sinzig, Rhineland-Palatinate. The line components we employ also come from German or European sources. All components are optimally matched to each other. They are compact and appealing in design. The plant components have been optimised for flexibility and were designed with maintenance access to the installed components in mind. The FEDDEM-LFT plant is equipped with an industry-4.0-compatible control system. Upon customer request, all relevant production parameters can be supplied to the customer’s production planning system.
Masterclass
German LFT Masterclass - Powerful Extrusion, Elegant Process
Disclaimer: All specifications and information given on this website are based on our current knowledge and experience. A legally binding promise of certain characteristics or suitability for a concrete individual case cannot be derived from this information. The information supplied here is not intended to release processors and users from the responsibility of carrying out their own tests and inspections in each concrete individual case.