Technical Details
LFT Pultrusion Plants
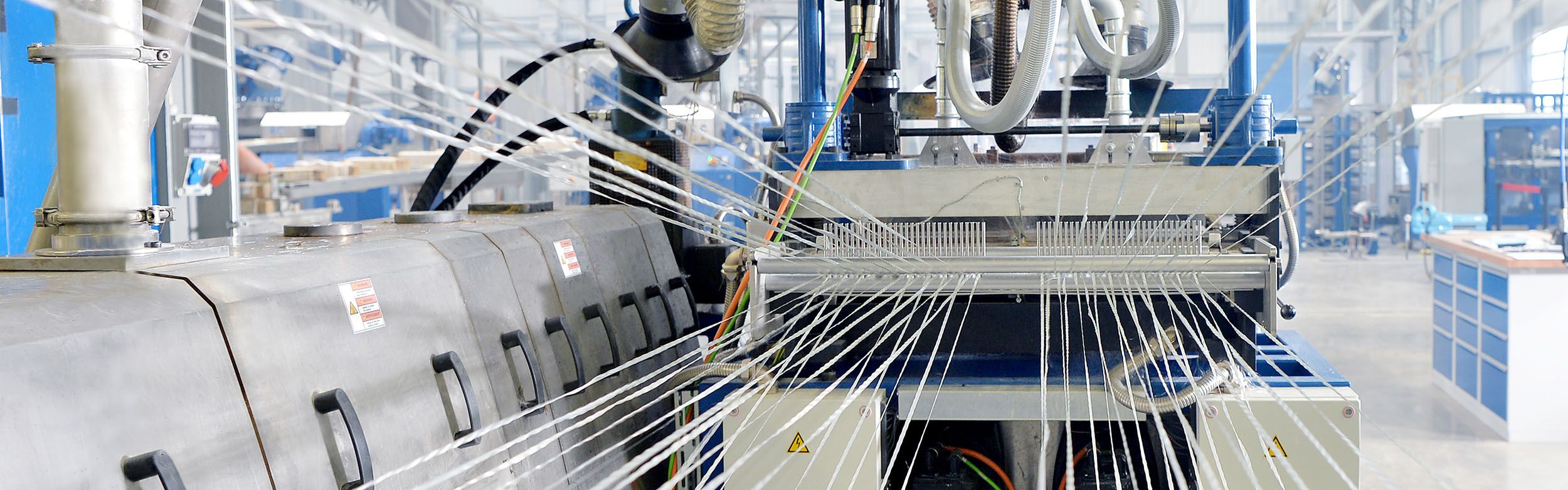
Production of High-performance Materials
Practice-oriented Optimisation of LFT Pultrusion Line Technology
The technology of LFT pultrusion lines for the production of long pellets has been around for several years. FEDDEM has taken a fresh look at the details of the line components to improve performance, product quality and handling. The result is not only unprecedentedly tight tolerances of the fibre content in the pellets but also a high repeatability of the achievable material properties of the LFT compound produced on different FLF-PT lines and line sizes with haul-off speeds of up to 60 m/min.
This was made possible, among other things, by employing a patented, modular impregnation die. The extruder for melt preparation is installed parallel to the roving line, which allows for considerable savings in the width required for installation of the line. All maintenance access points for the individual line components have been designed to allow for direct and fast access to ensure the highest possible line availability.
Image dimensions not found
Change image or reupload it
The Tensioner
The tensioning device developed by FEDDEM supports quick threading of the strands when starting up the line. The tensioner reliably preheats the glass fibre filaments in the rovings before they enter into the impregnation die. Uniform preheating is a prerequisite for excellent product quality at higher strand speeds.
Image dimensions not found
Change image or reupload it
Consistently High Product Quality
The impregnation die developed by FEDDEM enables high precision in melt distribution across the entire width of the die plate. This uniform distribution succeeds in minimising the fluctuations in the polymer-to-glass ratio that may occur on the outer strands. This results in tight tolerances in the glass-to-polymer ratio in the finished material.
Image dimensions not found
Change image or reupload it
Optimised Line Control
The system control offers optimisation functions in various areas, which, for example, largely compensates for fluctuations in the sizing of the fibre rovings by adjusting the process parameters, accordingly. This stabilises the average product quality to an unprecedented extent.
Image dimensions not found
Change image or reupload it
Flexibility in Production Capacity Through Modular Design
Thanks to the modular design of the patented FIE impregnation unit, a 58-strand line can be temporarily run with 29 strands without major conversions – e.g. for producing sample material of another LFT product.
Image dimensions not found
Change image or reupload it
Flexibility in processing different polymers
Different cooling methods are preferable depending on the type of polymer and the target fibre/polymer ratio. Accordingly, the FEDDEM FKS cooling zone has a modular structure and can be adjusted in length or can be operated with different cooling media as required.
Image dimensions not found
Change image or reupload it
Minimised Changeover Times in the Creel
Depending on the strand speed during the production of LFT compounds, the roving bobbins run empty sooner or later. At higher strand speeds, the production time to the next roving change is often only a few hours. The line then must be stopped to change the bobbins. Thanks to a specially developed procedure, the roving changes on FLF-PT lines can be carried out up to 50 % faster than with conventional methods.
Would you like to learn more about our LFT system?
Arrange an online appointment with our LFT experts. Free of charge and without obligation, of course.
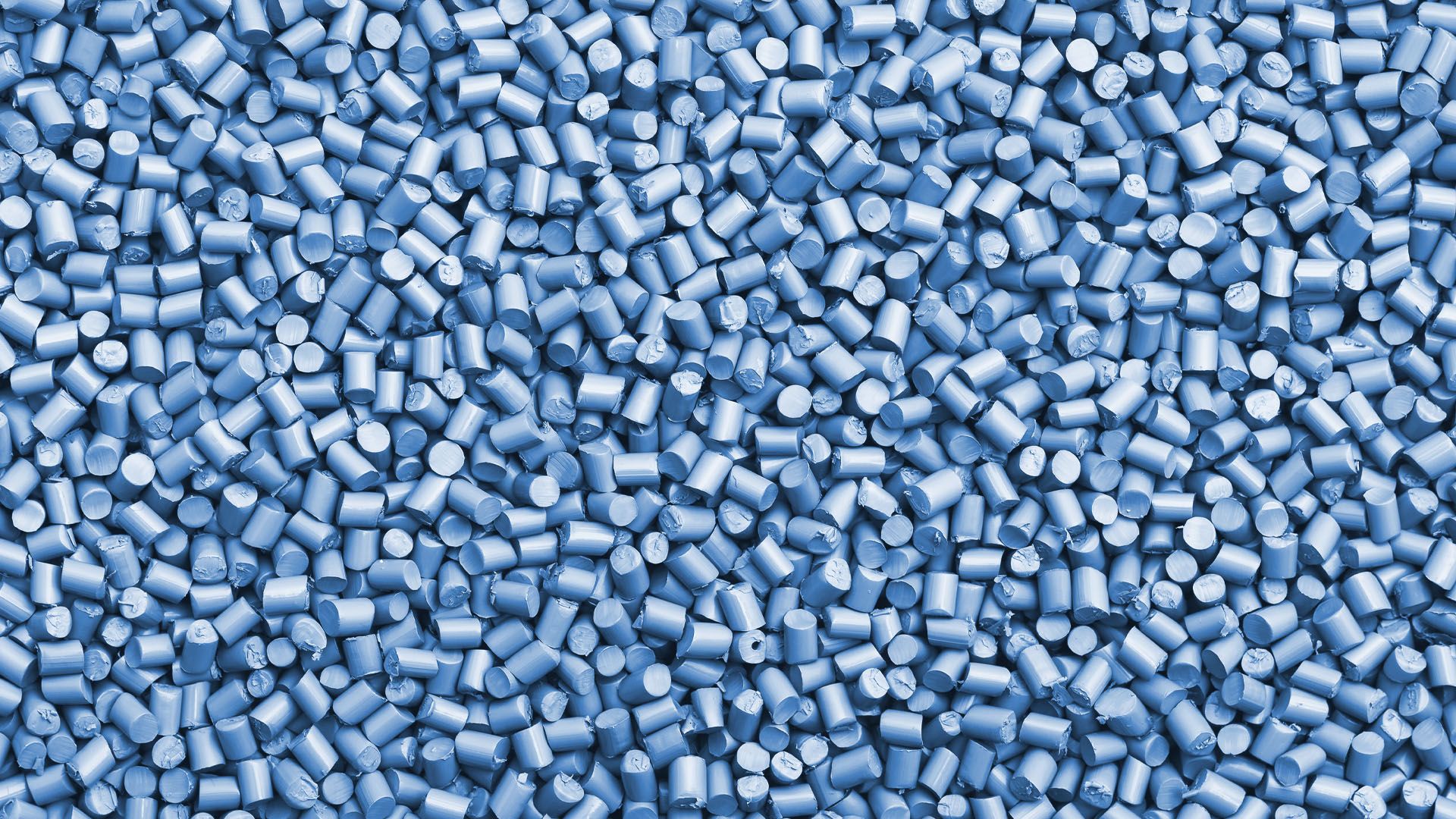
LFT Pultrusion for Engineering Plastics
Special Challenges
Polyolefins such as PP require a sufficiently long cooling distance before pelletising at high haul-off speeds
When processing engineering plastics, the melt reacts much more sensitively with regard to the residence time at higher temperatures
Avoiding “dead areas” in the melt channels and preventing local overheating becomes more important in minimising melt degradation
Engineering plastics usually require higher processing temperatures than polyolefins
Engineering plastics require increased complexity in the impregnation process
Uniform distribution of the melt over the entire width of the impregnation die is generally more challenging with engineering plastics than with polyolefins
More information
Learn more about FEDDEM
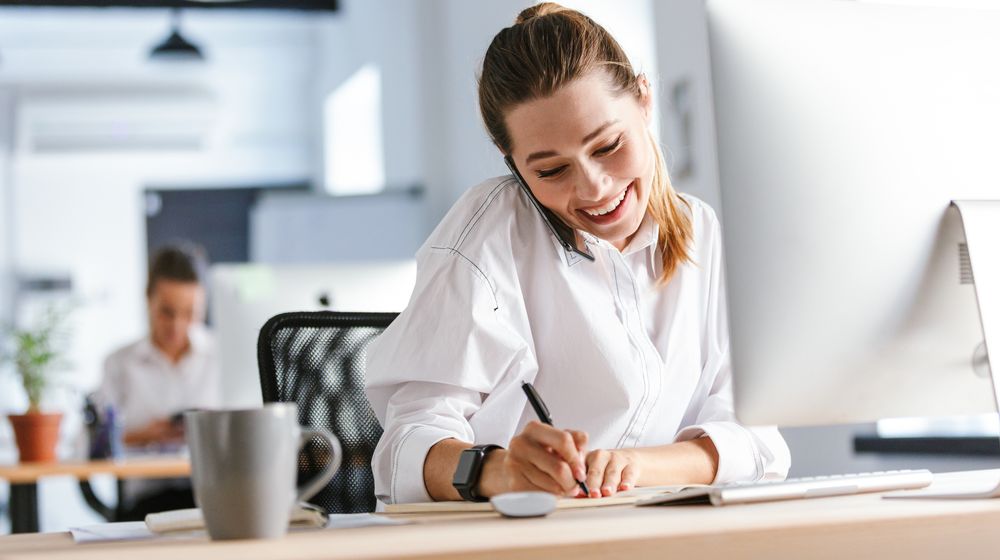